在医药、食品及精密包装领域,铝塑泡罩包装因其高阻隔性、便携性和可视性被广泛应用。然而传统人工或半自动投料方式存在效率低、精度差、浪费严重等问题。本文以自动称重系统为核心,探讨其在铝塑泡罩生产线中实现精准投料的技术路径、优势及实践案例,并提出智能化升级方向,为行业提升生产效能与质量控制提供参考。
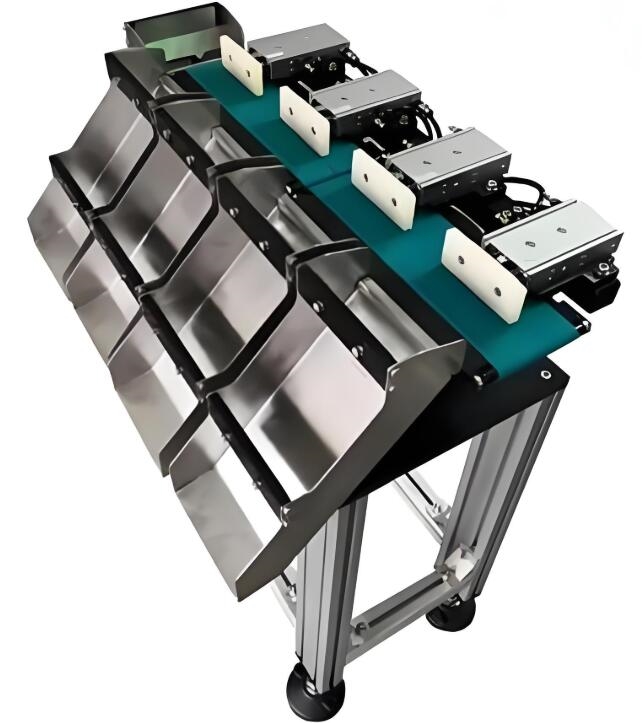
一、铝塑泡罩包装工艺与投料挑战
铝塑泡罩包装的工艺流程通常包括:铝塑复合膜放卷→加热成型→物料投放→热封→裁切→输出成品。其中,精准投料是核心环节,直接关系到产品剂量准确性、稳定性及生产成本。传统工艺的痛点包括:
1、人工投料误差大:依赖人工目测或经验判断,易出现物料过量或不足,导致产品不合格率上升。
2、效率瓶颈:人工操作速度受限,难以匹配高速自动化生产线需求(如每分钟60~120泡罩)。
3、物料浪费:过量投料造成原料损耗,尤其在高价值药品或保健品生产中,成本压力显著。
4、数据追溯困难:人工记录投料量缺乏实时性与准确性,难以满足GMP(药品生产质量管理规范)要求。
在此背景下,自动称重系统的引入成为解决上述问题的关键技术。
二、自动称重技术原理与组成
1、系统核心功能
自动称重系统通过实时监测投料重量、动态调整投料量,并与泡罩成型工艺同步联动,实现“精准投放”目标。其核心技术包括:
- 高精度称重模块:采用应变片式传感器或电磁力传感器,分辨率可达0.01g,适应微量投料需求。
- 动态补偿算法:通过PLC或工控机实时计算投料误差,结合物料特性(如流动性、密度)进行动态补偿。
- 闭环控制系统:与伺服电机、气动阀门联动,实现“称量-投放-反馈”的快速循环,响应时间≤100ms。
2、系统组成架构
- 称重单元:包括称重斗、传感器、振动马达(防止物料滞留)、清洁吹扫装置。
- 控制单元:PLC主控系统+HMI人机界面,支持参数设定、数据存储与异常报警。
- 执行机构:伺服驱动的投料阀门或螺杆计量装置,确保物料均匀下落。
- 视觉检测模块(可选):通过高速相机拍摄投料过程,辅助判断物料分布状态。
3、与泡罩机协同机制
系统需与铝塑泡罩成型设备深度集成:
- 信号同步:接收泡罩成型机的“模具到位”信号后启动投料,避免物料散落。
- 速度匹配:根据生产线速度(如每分钟80次)动态调整投料节奏,确保每个泡罩独立计量。
- 温度补偿:结合热封温度数据,修正物料因环境温差导致的体积变化。
三、自动称重系统的应用优势
1、精准性提升:
- 投料误差可控制在±0.5%以内(如1g物料误差≤0.005g),远超人工操作精度。
2、效率倍增:
- 单次投料周期缩短至0.3~0.5秒,匹配高速泡罩线生产节拍。
- 人工成本降低70%以上,尤其适用于大批量、连续性生产场景。
3、质量稳定性:
- 消除人为因素干扰,避免因疲劳或操作差异导致的剂量波动。
- 数据实时上传至MES系统,支持批次追溯与工艺优化。
4、合规性保障:
- 符合FDA、GMP等法规对数据完整性的要求,投料记录自动存档,支持审计追踪。
- 模块化设计便于清洁验证,避免交叉污染风险。
自动称重系统在铝塑泡罩线中的应用,标志着包装生产从“经验依赖”向“数据驱动”的转型。通过技术创新与工艺优化,企业可显著提升产品质量、降低运营成本,并为智能化工厂建设奠定基础。